Extreme enclosure heli-lifted into an extreme environment
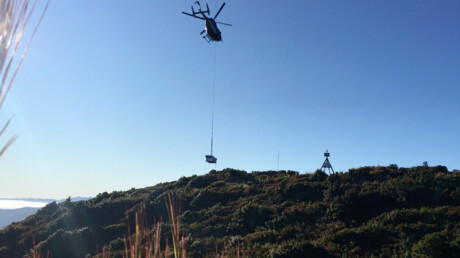
Dennis Hill and his crew at Ventech Systems recently designed and developed a massive enclosure that was installed on the peak of Mt Wainui, on the Kāpiti Coast of New Zealand’s North Island, where it will support Wellington Regional Council’s critical communications equipment. With a weight of 2300 kg and a size of 4.9 m3, the enclosure was specifically engineered for conditions on the 722-metre-high mountain peak, and comes equipped with a modern, climate-friendly energy solution.
“This site is off-grid and the weather is harsh, yet all critical communications equipment needs to work 24/7 without any issues or hiccups due to rain, ice, dust, insects or heat,” said Hill, who has 20 years’ engineering experience.
People from all sorts of organisations have visited Ventech’s Wellington workshop, where Hill and the team are always ready to solve their clients’ individual needs. In the case of the Mt Wainui enclosure, that was commissioned by Dave Rangi from Tait Communications.
“I’ve been in business for 30 years plus and we went searching for a reliable enclosure to house our gear; Dennis’s name came up,” Rangi said. “His services are not only his patented ventilation and temperature-controlled systems within his enclosures, he also designs and manufactures individually to customers’ specifications. The major issue for us was that the cabinet needed to be heli-lifted into place to an off-grid location, and with a gross weight of 2300 kg.”
Ventech Systems designed the enclosure around the footprint of the critical communications equipment and batteries that required housing. The mast had to be incorporated in the build of the plinth.
“We had to manufacture everything so it was collapsible for transport without exceeding the maximum lift of the helicopter (1000 kg),” Hill said. “The enclosure had to be able to house 960 kg of batteries, the EFOY and 240 L of methanol, including the high-tech radio equipment. There was a lot of calculation involved beforehand. Also, heavy weight tends to start spinning hanging below a helicopter, so I made amendments to that as well to stabilise the load in flight.”
The engineer brought the cabinet to Tait to add some of the equipment and all the cables. Checking the load at a weigh station, he made sure the maximum lifting capacity of the helicopter wasn’t exceeded.
“Dennis even got us the certification for the heli-lift,” Rangi said. “He did a fantastic job and helped us with lots of input we hadn’t even thought of before.”
The 4.9 m3 enclosure was flown in by helicopter and landed safely on the installation pad. A second lift brought in the batteries.
“By calculation and maximising each load, we could minimise the heli-lifts required, equating to a saving on transport costs,” Hill concluded.
Phone: +64 4 589 5969
Semtech AirLink XR60 5G router
The Semtech (Sierra Wireless) AirLink XR60 5G router is fully certified for critical...
Omnitronics omniGateP25 and omniGateDMR RoIP gateways
Omnitronics' omniGateP25 and omniGateDMR digital radio gateway products, designed to provide...
RuggON SOL 7 12″ rugged Windows tablet for field applications
The RuggON SOL 7 is a 12″ fully rugged Windows tablet powered by Intel Arrow Lake Core...